Generación de calor
La mayoría de los componentes electrónicos convierten la energía eléctrica en calor, en mayor o menor cantidad, dependiendo de sus características o régimen de funcionamiento.
Si este calor no se transfiere correctamente al medio ambiente, el componente se calienta más allá de los límites previstos y puede "quemar".
Los radiadores o disipadores térmicos son los elementos que ayudan a realizar esta transferencia, por lo que es muy importante en las Asambleas electrónicas. Analicemos su función.
Cuando una corriente eléctrica debe superar una resistencia a su circulación, es decir, se encuentra con una oposición, el resultado del "esfuerzo" de su paso es la producción de calor. La energía eléctrica se convierte en calor y esto es válido para la mayoría de los componentes electrónicos comunes.
El calor liberado en este proceso tiende a calentar el componente y como resultado de la diferencia de temperatura que se establece entre él y el medio ambiente, comienza una transferencia de calor a este ambiente, como se muestra en la figura 1.
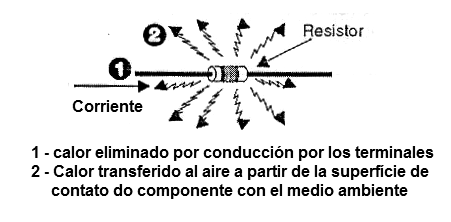
La diferencia de temperatura entre el componente y el entorno determina la velocidad a la que se transfiere el calor generado. Así que llega un momento en que el calor generado y la transferencia es igual, cuando entonces la temperatura del cuerpo que lo genera se estabiliza.
La transferencia de calor generado al medio ambiente depende de varios factores como la superficie de contacto del componente con el medio ambiente, La capacidad que tiene para impulsar el calor desde el punto en el que se genera hasta el punto de contacto con el medio ambiente y, finalmente, la diferencia de temperatura entre estos dos puntos.
Podemos comparar la diferencia de temperatura entre el punto donde se genera el calor (componente) y el ambiente (aire que lo rodea) como la diferencia de potencial eléctrico entre los dos puntos.
El flujo de calor entre los dos puntos es hecho por una ruta de una manera similar a una corriente. Así que tenemos un circuito "térmico" en el que hay una "resistencia" que debe ser superada por el calor para llegar al medio ambiente.
Si la resistencia es alta, es que hay dificultades para el calor generado en una pastilla de un componente, por ejemplo, un transistor o un circuito integrado, para llegar al medio ambiente, su temperatura aumenta, porque debería haber "mayor tensión" para que el calor salga, Ganando la oposición encontrada.
Vea que con el aumento de la "tensión" que en el caso es la temperatura, tenemos mayor "presión" y con esto aumenta el flujo de calor, por lo que viene un Instante se produce el equilibrio de la situación: la cantidad de calor generado es igual a la cantidad de calor transferido al medio ambiente.
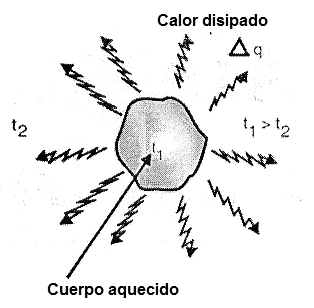
En electrónica, debemos tener cuidado de que esto ocurra a una temperatura que no comprometa la integridad del componente.
Por ejemplo, el silicio utilizado en la mayoría de los dispositivos semiconductores como diodos, transistores y circuitos integrados no puede calentarse a una temperatura superior a 125 grados centígrados., llegando en algunos casos a 150°C.
La mayoría de los componentes están equipados con recursos que facilitan la conducción del calor generado a su superficie y por lo tanto al medio ambiente.
Sin embargo, muchos componentes no tienen dimensiones suficientes para hacerlo solos, es decir, tienen una superficie de contacto insuficiente para que el calor generado pueda transferirse fácilmente.
Esto se debe a que uno de los factores que influyen en la transferencia de calor de un medio a otro es la superficie de contacto entre estos dos medios.
Sus pequeñas dimensiones previenen más de unos pocos centenares de miliwatts y eventualmente algunos watts de potencia se convierten en calor y se transfieren (se disipan) al ambiente eficientemente.
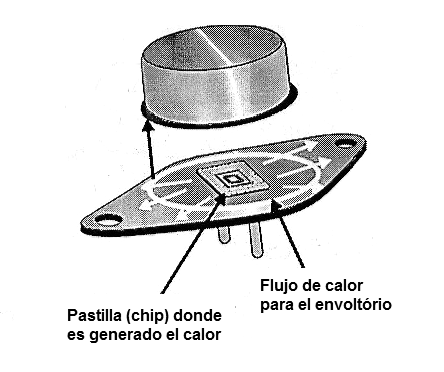
¿Cómo obtener estos componentes para transferir al medio ambiente todo el calor generado para que su temperatura no suba más allá de los límites permitidos?
Teniendo en cuenta que el calor generado puede ser transferido al medio ambiente de tres maneras, irradiación, contacto y convección, tenemos las siguientes posibilidades:
Contacto
Los metales son buenos conductores de calor. Así, el montaje de componentes electrónicos en contacto con superficies metálicas más grandes, siempre y cuando no haya contacto eléctrico, pero sólo térmico, ayuda en la transferencia de calor.
Por lo tanto, para los transistores de tamaño pequeño, de potencia media, MOSFETs, SCRs y los mismos circuitos integrados, una solución al problema de la transferencia de calor es montarlos contra una superficie metálica más grande, capaz de ayudar a absorber y transferir al medio ambiente el calor generado.
En la figura 4 tenemos una solución equipada para el caso de transistores de potencia media como el BD135 y TIP31 cuando no operan con su potencia máxima.
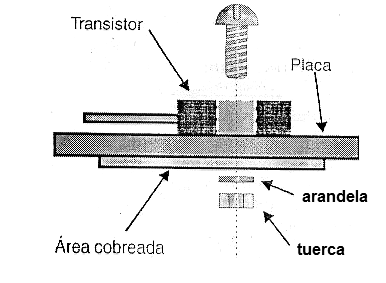
En este caso, ensamblamos el transistor en contacto con un área cubierta más grande de la placa de circuito impreso, que ayuda a absorber el calor generado, y como tiene una superficie más grande del contacto con el aire que transfiere este calor al ambiente.
Podemos decir que la placa de circuito impreso se puede utilizar como radiador de calor en este caso.
Convección
El componente caliente transfiere calor al aire ambiente que luego se calienta.
El aire caliente es más ligero que el aire frío que te rodea y por lo tanto tiende a subir. Luego hay una corriente de aire caliente elevándose sobre el componente que "toma el calor" hacia arriba.
En aparatos de alta potencia es importante dejar los orificios de ventilación para que este aire caliente sea expulsado. A continuación, tenemos agujeros por debajo de donde el aire frío y los agujeros entran a través del aire caliente.
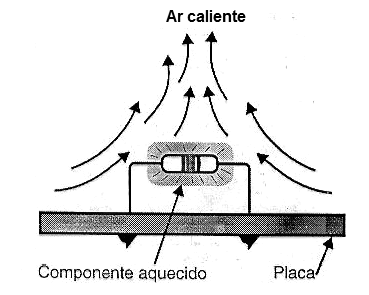
Podemos aumentar la capacidad de transferir calor al ambiente forzando la ventilación, que se puede hacer con la ayuda de un ventilador.
Esta característica es ampliamente utilizada en los equipos de alta potencia y fuentes de alimentación, o incluso en microprocesadores y microcontroladores que tienen ventiladores de enfriamiento que fuerzan la circulación de aire a través de los componentes de calefacción.
Incluso hay "micro ventiladores" (fans )que se pueden instalar sobre circuitos integrados y componentes especiales para ayudar a disipar el calor que genera, como vamos a vea más.
Irradiación
Parte del calor generado por cualquier cuerpo se irradia en forma de ondas electromagnéticas. Una buena parte de esta radiación está en la gama infrarroja y para su propagación no hay necesidad de un medio material.
Resulta que los cuerpos negros irradian mucho mejor calor que los cuerpos de otros colores.
Por esta razón, los componentes pintados en negro tienen una mayor capacidad de irradiación de calor que los equivalentes con cubiertas de color más claras, como se sugiere en la figura 6.
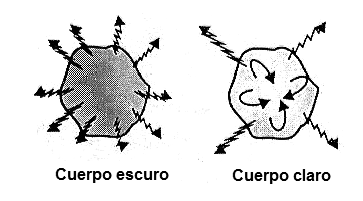
Ley de Joule
Cada dispositivo electrónico, que no presenta una resistencia cero, genera una cierta cantidad de calor cuando es atravesado por una corriente eléctrica.
En el caso de una resistencia, la energía eléctrica desarrollada que se convierte en calor es determinada por la Ley de Joule.
Lo que establece esta ley es que la cantidad de calor generado, o potencia disipada (medida en watts), es proporcional al producto de la corriente por la tensión en la resistencia, según la fórmula:
P = V x I (1)
Donde:
P es la potencia en watts (W)
V es tensión en volts (V)
I es la corriente en ampères (A)
Teniendo en cuenta que por Ley de Ohm que la corriente en un resistor es proporcional a la tensión en sus terminales o R = V/I, también podemos escribir a la Ley de Joule que:
P = R x I2 (2)
P = V2/r (3)
Muestra del Cálculo:
Calcule la potencia disipada por una resistencia de 10 ohm cuando está conectada con un generador de 12 volts.
Resolución: como tenemos la tensión y la resistencia, usamos la fórmula (3).
P = (12 x 12) / 10
P = 144/10
P = 14,4 watts
Puesto que el dispositivo de la resistencia es nula e ideal, no existiendo en la práctica, podemos decir que todos los dispositivos atravesados por la corriente en un circuito verdaderamente generan calor.
Así, los semiconductores de la potencia tales como transistores bipolares, MOSFETs, IGBTs, SCRs, triac, etc., en el estado de conducción generan calor.
Dado que no son perfectos, siempre presentando una cierta resistencia, la cantidad de calor generado dependerá de la intensidad de la corriente y de esa resistencia.
Como esta resistencia causa una caída de tensión en el dispositivo, podemos decir que la potencia generada es dada por el producto de esta caída de tensión por la intensidad de la corriente del LED.
El calor generado por los dispositivos debe disiparse de manera que no provoquen elevaciones de temperatura capaces de dañarlos.
A medida que estudiamos en los capítulos anteriores, todos los componentes semiconductores tienen límites de disipación y temperaturas máximas en las que pueden operar.
Esto significa que estos dispositivos, en condiciones normales de funcionamiento, no disipan el calor máximo que el fabricante prevé para una aplicación típica.
En tales casos, el dispositivo debe depender de recursos adicionales para disipar el calor generado, es decir, con disipadores térmicos.
El disipador térmico
Para los casos en que el calor generado es grande, necesitando ser transferido al ambiente de modo que el componente no tenga su temperatura pasando los límites que tolera, deben ser usados medios auxiliares.
Así, además de los recursos que permiten difundir el calor por la propia placa de circuito impreso, a través de los materiales, la ventilación forzada, el medio principal, sin duda es lo que hace uso de radiadores o disipadores térmicos.
Estos elementos disfrutan los tres modos de transferencia de calor al medio ambiente.
Así, la cantidad de calor que un radiador de calor puede transferir al medio ambiente depende básicamente de los siguientes factores:
Tamaño
De hecho, lo que hay que tener en cuenta es la superficie del radiador de calor que tiene contacto con el medio ambiente. Para aumentar esta superficie, los radiadores están construidos con muchos pliegues o aletas, como se muestra en la figura 7.
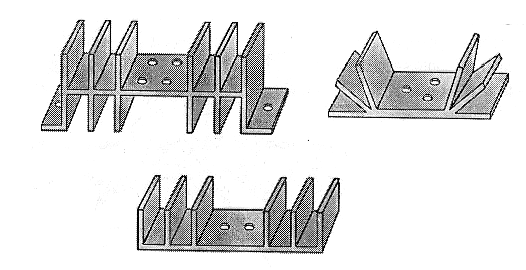
Entonces vale la superficie de contacto de todas las aletas con el medio ambiente.
Una superficie muy grande se obtiene incluso utilizando un componente que ocupa un volumen relativamente pequeño, tal como lo entendemos en el tipo que se muestra en la figura 7.
Para los casos en que la potencia que se va a disipar no sea tan grande, una sola plancha plana conectada al componente, o incluso plegada en forma de "U" o "L", ya puede dar resultados satisfactorios, como se muestra en la figura 8.
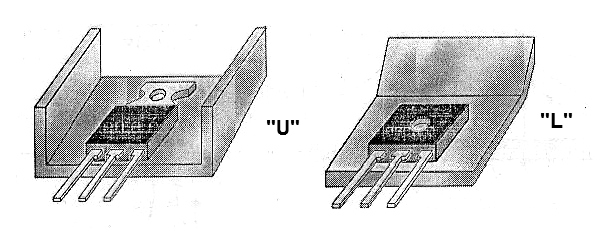
Vea que si observamos el calentamiento excesivo de un componente esto realmente significa que el calor producido no está siendo transferido al ambiente y esto puede no ser solamente debido al radiador.
Contacto
Debe haber un contacto físico que facilite la transferencia de calor entre el componente y el radiador. Para mejorar este contacto, varios son los recursos que se pueden utilizar.
Una de ellas consiste en el uso de una pasta térmica que está hecha de silicona, un buen conductor de calor. Tanto el componente como el radiador se engrasan con esta pasta antes del montaje, como se muestra en la figura 9.
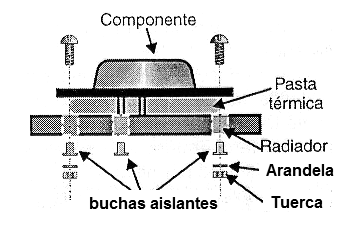
Vea que en los casos en que el componente se debe aislar del radiador, debemos colocar entre él y el radiador un elemento aislador apropiado.
Este aislante se puede hacer de mica o de un plástico especial, buen conductor de calor, pero eso no conduce la corriente eléctrica, como se muestra en la figura 10.
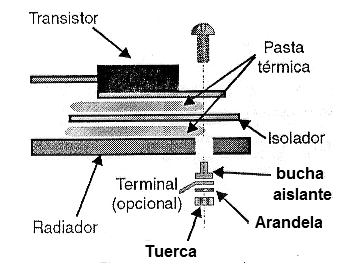
Irradiación
Los radiadores oscuros son más eficientes que los claros en la transferencia de calor al medio ambiente. Vea que, si la transferencia por contacto ya es eficiente y hasta que haya la ayuda de la ventilación, el uso de un radiador claro no cambia en gran medida la eficiencia del sistema.
Esto ocurre porque parte del calor se irradia en forma de ondas electromagnéticas, concentrando principalmente en la gama infrarroja.
Es parte de las propiedades de los cuerpos negros que son radiadores ideales, para elegir materiales que puedan ser utilizados eficientemente de esta manera para deshacerse del calor generado por los componentes.
La Ley de Stefan-Boltzman muestra cómo la radiación producida por un cuerpo negro caliente se distribuye a través del espectro.
Ventilación forzada
También debemos recordar los casos en que la cantidad de aire en contacto con las aletas que deben transferir el calor puede aumentar apreciablemente con el uso de la ventilación forzada, como ocurre en el caso del uso de "fans", muchos comunes en los dispositivos que requieren una grande tasa de transferencia de calor, caso de la caja de microprocesadores.
En la figura 11 tenemos un disipador con fan o cooler (ventilador).
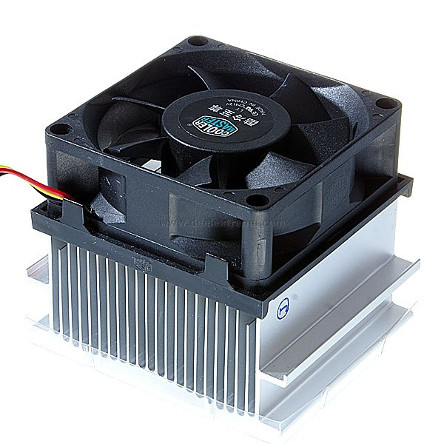
Un tipo de disipador térmico que tiene más y más uso frecuente es lo que emplea un dispositivo de Efecto Peltier.
Este dispositivo, que se muestra en la figura 12, cuando está accionado por una tensión continua retira el calor de una de los lados y lo lanza en el otro que es un disipador común con un ventilador convencional.
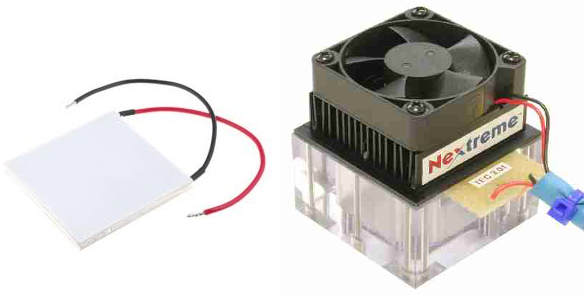
Otro tipo de disipador térmico con transferencia de calor forzada es lo que utiliza el agua o el aceite para este propósito. En la figura 13 tenemos un ejemplo.
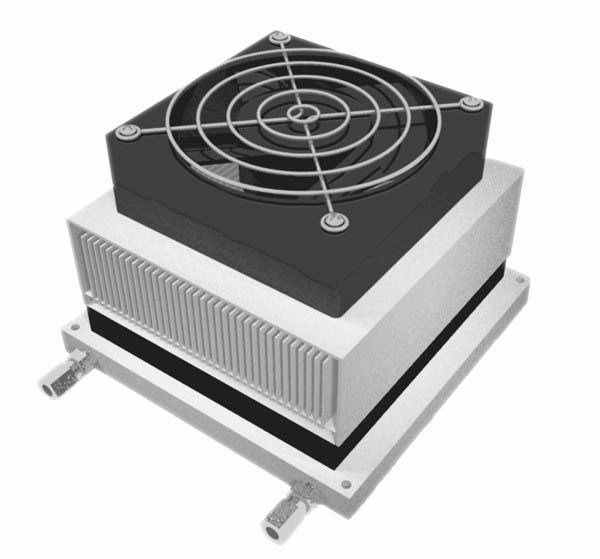
El circuito térmico
Cuando conectamos un radiador de calor a un dispositivo que genera calor, la temperatura final del dispositivo dependerá de la cantidad de calor que genera, la velocidad con la que el dispositivo puede transferir el calor generado, y la temperatura final del ambiente al que se transfiere el calor.
Podemos compararlo con un "circuito térmico" en el que la diferencia de temperatura es el "tensión" responsable del flujo de calor de la fuente (componente) al medio ambiente.
El flujo de calor es la "corriente" y la capacidad que los distintos elementos del circuito tienen para llevar este calor es la "resistencia térmica".
Así como se muestra en la figura 14 podemos elaborar un "circuito térmico" que siga una Ley muy similar a la Ley de Ohm, en esa medida, que podemos llamar sin problemas de " Ley de Ohm Térmica".
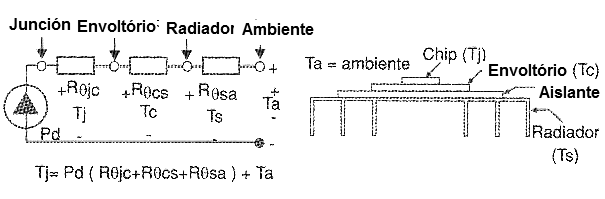
Para el desarrollador es necesario diseñar este circuito para que, en una transferencia de calor normal, con los recursos utilizados, la temperatura del componente permanezca siempre por debajo de los máximos permitidos.
Y, esto debe tener en cuenta que la temperatura final, que es la temperatura ambiente, puede variar entre ciertos límites.
Peligros del sobrecalentamiento
Todos los componentes electrónicos, capacitores, inductores, transistores, dispositivos semiconductores, etc. tienen las temperaturas máximas de operación especificadas por los fabricantes.
La fiabilidad y eficiencia de un componente disminuye a una velocidad muy alta cuando la temperatura aumenta.
Por cada 10 ó 15°C de aumento de temperatura, por encima de 50 ° C la tasa de avería de un componente plegable.
Además, ellos componentes electrónicos de se comportan diferentemente cuando la temperatura sube.
Los capacitadores, por ejemplo, empiezan a tener una tasa de evaporación del electrólito mucho más significativa que reduce la vida útil del componente.
Los componentes magnéticos presentan pérdidas mucho mayores cuando la temperatura pasa de 100°C en muchos de ellos la degradación del aislamiento puede ocurrir de una manera aguda.
Para los semiconductores tenemos varios problemas a considerar cuando la temperatura sube.
Por esta razón es que, estudiando varios componentes en capítulos anteriores dimos especial atención a SOA (área de operación segura), alertando al lector sobre los peligros de no respetar sus límites
Un de los problemas que se producen con la calefacción, y que estudiamos en el caso de los diodos, es la división desigual de las corrientes y por lo tanto De la potencia en los componentes que están conectados en serie o en paralelo.
Este problema puede llevar a un efecto de "avalancha", como se muestra en la figura 15, en el cual uno de los componentes se puede traer a una calefacción más alta irreversible hasta quemarse.
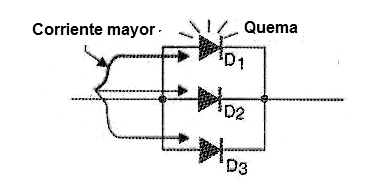
En ciertos semiconductores también tenemos la reducción de las tensiones de ruptura. La corriente de la salida aumenta y los tiempos de la conmutación también.
Mientras que controla las tensiones y las corrientes en los dispositivos, el uso de los componentes que se diseñan bien para asegurar flujo de calor excelente dentro de ellos ayuda a reducir al mínimo los problemas de la disipación de calor, el desarrollador tiene la responsabilidad de montar el componente en disipadores eficientes cuando se hace necesario.
En este caso, hay que tener en cuenta dos factores:
El montaje del disipador térmico requiere el uso de tornillos y tuercas, aisladores y eventualmente grasa térmica.
El diseño del radiador que no sólo debe tener la capacidad de disipar el calor generado como se coloca correctamente en un lugar donde usted puede hacer esto eficientemente.
Calcular con la resistencia térmica
Como hemos visto, el proceso que va desde la generación de calor por parte del componente, su transmisión a través de medios apropiados hasta la disipación en el medio ambiente implica un circuito térmico.
Así como se muestra en la figura 16, en el caso de un dispositivo semiconductor tenemos varios elementos en este circuito, que pueden considerarse como estratificados.
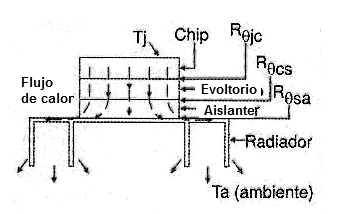
El circuito térmico equivalente a la estructura indicada en la figura 16 se muestra en la figura 17.
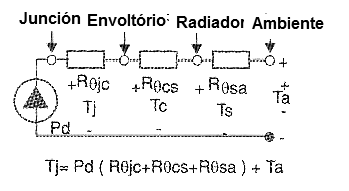
Vea que los elementos se comportan como resistores, lo que significa que, si hay caminos paralelos al flujo de calor, pueden ser considerados como "resistores térmicos" conectados en paralelo.
Impedancia térmica transitoria
De la misma manera que en un circuito eléctrico una temperatura transitoria, es decir, una producción de un pico de calor por el componente que genera un pico de calor puede causar daño al dispositivo si no se absorbe rápidamente, evitando que la temperatura suba en el mismo nivel velocidad, como se muestra en la figura 18.
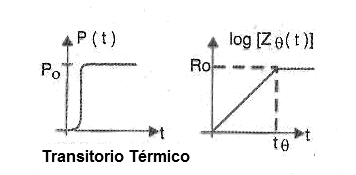
El componente térmico equivale a un capacitor, que absorbería un pico eléctrico.
En el caso del calor está representado por la capacidad térmica del sistema.
Entonces podemos hablar de la capacidad térmica por unidad de volumen:
Cv – dQ/dT (Joules / °C) que puede absorber el calor en un circuito equivalente que se muestra en la figura 19.
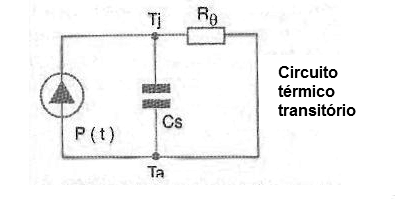
Así, el circuito térmico equivalente será: Cs = Cv x V donde es V es el volumen del componente.
A continuación, llegamos a la Impedancia Térmica Transitoria del circuito que se da por la fórmula junto a la figura 20.
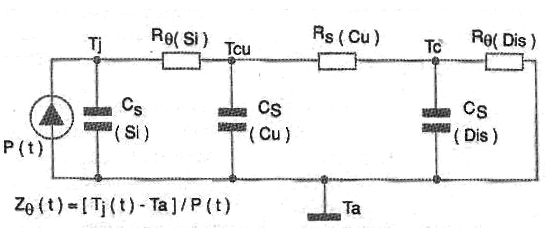
Vea que podemos hablar de un tiempo térmico constante para este circuito que será dado por:
Tθ = π x Rθ x Cs / 4
Si disponemos de una estructura multicamadas, podemos asociar a las distintas capacidades térmicas de sus elementos "capacitancias térmicas" en el circuito que se muestra en la figura 21.
Es el caso de un sistema formado por diversos tipos de materiales tales como silicio, cobre, y el disipador sí mismo.
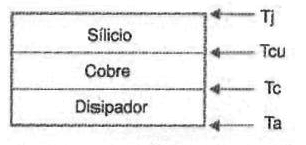
Los disipadores en la práctica - Cómo elegir
El tipo de disipador de corriente más común disponible para el uso en circuitos electrónicos es el que se fabrica en aluminio.
Muchos tienen una capa anodizada de óxido oscuro que pretende reducir la resistencia al calor hasta en un 25%.
Los disipadores de calor comunes enfriados por convección sin ser forzados tienen una constante de tiempo térmico típica que oscila entre 5:15 minutos. Las constantes de tiempo de los disipadores térmicos con ventilación forzada son mucho más pequeñas.
Los siguientes son los factores que determinan la elección de un radiador de calor para una aplicación particular:
Potencia máxima que debe ser disipada por el componente montado en el disipador térmico. Pdis)
Temperatura interna máxima del componente - temperatura de la juntura (TJ, máximo)
Resistencia térmica de la juntura componente para su cubierta (R?j)
Temperatura ambiente máxima (TA, máx.)
La fórmula para aplicar será:
Rsa = (Tj, máx. – Ta, máx.) x Pdis – Rθj
Pdis y Ta, máx. están fijos para su aplicación mientras que Tj, máx. y Rθj son determinados por el fabricante del componente.
A partir de entonces de esta Idea que cualquier cuerpo que conduzca e irradia calor puede funcionar como radiador de calor podemos tener varias técnicas para la construcción de disipadores para uso en aplicaciones electrónicas.
La mayoría de los tipos tienen en la circulación de aire la transferencia de la mayor parte del calor generado.
Los tipos principales, que se muestra en la figura 22 son:
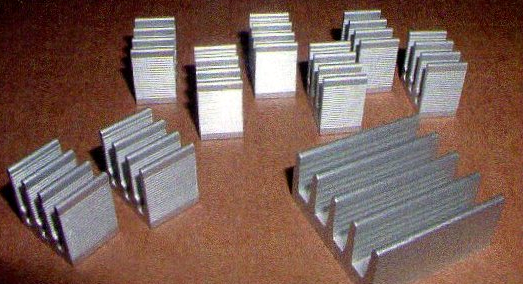
a) Estampados – son disipadores térmicos formados de hojas de cobre o de aluminio, estampados para adquirir el formato deseado. Este tipo de disipador térmico es ampliamente utilizado en la mayoría de los aplicaciones electrónicos porque son baratos y fáciles de fabricar.
b) Por extrusión – son los más comunes en aplicaciones de potencia tales como fuentes de alimentación, amplificadores, etc. El proceso de extrusión facilita la obtención de formatos bidimensionales con la capacidad de disipar grandes cantidades de calor. Además, se pueden cortar y trabajar de una variedad de maneras. La posibilidad de cortar aletas en corte transversal permite la elaboración de patrones que permitan aumentar el rendimiento de 10 a 20%.
c) Juntas de Tiras prefabricadas – la limitación de la capacidad de disipación de los tipos de convección se puede eludir si se aumenta la superficie de contacto con el aire. La mayor exposición a la corriente de aire hace que sea más fácil transferir el calor generado. Tales disipadores son formados por las aletas de aluminio epóxido - pegadas a una base extrusión - hecha.
d) Fundido - arena, un núcleo y el proceso de fundición para los disipadores se puede hacer en aluminio sin la necesidad de vacío, cobre o bronce. Este tipo de disipador de aire tiene un mayor rendimiento en sistemas de ventilación forzada.
e) Aletas plegadas – el papel de aluminio o el cobre corrugado se utilizan para aumentar la superficie en contacto con el aire en este tipo de disipador térmico. El sistema se fija entonces a una placa que sirva como base o incluso pegada a la superficie donde el calor debe ser quitado.
Cómo Medir la Resistencia Térmica de un Disipador
El método descrito es empírico, sirviendo para determinar con exactitud razonable la resistencia térmica de un disipador térmico.
Todo lo que el lector necesita es un termómetro (preferiblemente el tipo de contacto digital) y una fuente de calor conocida. La fuente de calor puede ser un resistor de potencia o incluso un transistor, como se muestra en la figura 23 conectado a una fuente de tensión ajustable.
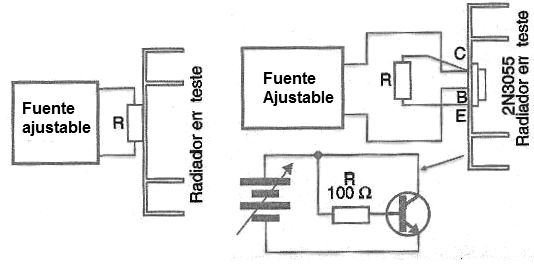
El resistor o el transistor debe poder proporcionar una buena potencia, por ejemplo, el 2N3055. Será interesante que, al determinar las características del disipador térmico, esté lo más cerca posible de las condiciones reales en las que se utilizará.
Por ejemplo, ya se puede fijar en la caja del aparato en el que se instalará para comprobar que el sistema de ventilación es eficiente.
Lo que usted hace entonces es ensamblar el disipador en contacto con el resistor o el transistor usado como fuente de calor. El contacto térmico perfecto es esencial para la precisión de las mediciones, como se muestra en la figura 24.
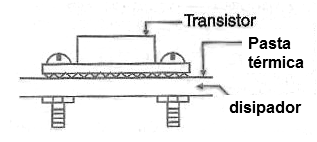
En el caso de un transistor es más fácil hacer este contacto, ya que podemos utilizar pasta térmica para este fin, como en el montaje final del componente que se usará.
Comience aplicando una pequeña potencia al resistor o al transistor y espere por lo menos una hora para que el equilibrio térmico ocurra.
Si el calor generado es insuficiente para calentar el disipador térmico (que todavía está muy frío), aumente la potencia y espere otra una hora hasta la estabilización. Vaya haciendo esto en etapas hasta que consiga una temperatura final del disipador térmico en el rango de 50 a 60°C aproximadamente.
Note la potencia generada por el Ph multiplicando la corriente en el circuito por la tensión. Observe la temperatura final medida en el disipador térmico (th) y la temperatura ambiente (ta). A continuación, podemos aplicar las siguientes fórmulas:
Variación de temperatura (tr)
tr = th – ta (1)
Donde:
th - temperatura del disipador térmico (°C)
ta – temperatura ambiente (°C)
Potencia disipada (aplicada al disipador térmico) – W
P = V x I (2)
Donde
P – Potencia aplicada y disipada en watts
V – tensión en el elemento calefactor (V)
I – Corriente en el elemento calefactor (I)
Finalmente tenemos la manera de encontrar la resistencia térmica en °C/W:
Rth = Tr/P (3)
Donde:
Rth – resistencia térmica en °C/W
Tr – variación de temperatura (°C)
P – Potencia aplicada/disipada (W)
Para obtener más precisión en los cálculos, el lector puede realizar la medición varias veces y tomar el promedio. En la mayoría de los casos, la determinación será razonable porque los propios fabricantes de disipadores especifican sus productos con una tolerancia que alcanza el 25% (¡por más y menos!).
Inercia Térmica
Como el calor generado no se transfiere al ambiente inmediatamente, necesitando un cierto tiempo de "tránsito" a través del disipador térmico, esto se traduce en una inercia térmica.
Se necesita tiempo para que el disipador de calor "responda" a las variaciones de temperatura del componente montado en él.
Esta inercia se debe principalmente a la masa del disipador térmico, que debe ser calentado, absorbiendo o consentir el calor cuando el aire ambiente o la temperatura del componente varía.
Cuanto más largo sea un disipador, más tiempo tardará en alcanzar la temperatura final de funcionamiento, como se muestra en el gráfico de la figura 25.
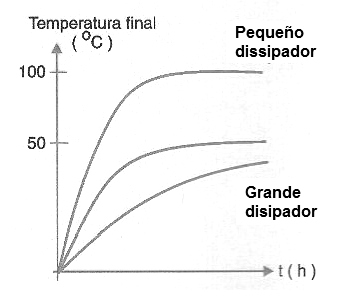
Vea entonces que un disipador térmico más grande no significa necesariamente que puede disipar más calor, pero más bien que toma más de largo alcanzar la temperatura del equilibrio.
Una gran inercia térmica puede ser interesante en algunas aplicaciones, ya que significa la capacidad de absorber el calor generado en los transitorios.
También debe ser atendido con excesiva inercia, ya que la temperatura del radiador puede tardar en elevarse actuando sobre un posible dispositivo de protección conectado a él, cuando la temperatura del propio componente ya ha alcanzado un valor capaz de causar su quema.
Montaje en disipadores de calor
En la figura 26, le mostramos cómo fijar un componente en cubierta TO-220 (plástico) en un disipador térmico. Entre el componente y el aislante y entre el aislante y el disipador térmico se debe colocar la pasta térmica.
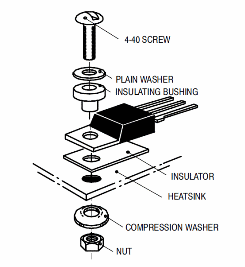
En muchos casos, el componente no debe tener contacto eléctrico con el disipador, ya que el tab (aleta) o cubierta metálica generalmente tiene una conexión con el colector de transistores o ánodo de SCRS. La prueba de contacto se muestra en la figura 27.
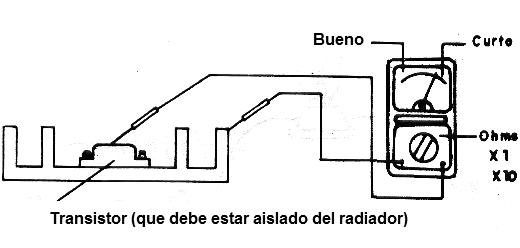
El contacto incorrecto (baja resistencia) puede causar cortocircuitos.
Para los circuitos integrados de alimentación de la cubierta DIL que tienen aletas de fijación del disipador térmico, el tipo de aleta con la guarnición de la placa, como se muestra en la figura 28, mostramos el procedimiento para montar un disipador y soldarlo junto con la placa.
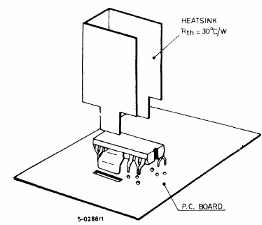
En la figura 29 tenemos la forma correcta de mantener el Cls SIL (Single in line) en los disipadores térmicos. Dependiendo de la aplicación se puede utilizar aislante de mica o plástico y todavía pasta térmica para ayudar en la transferencia del calor generado.
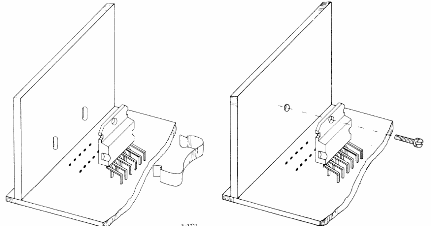